Plastic extrusion for efficient, scalable manufacturing solutions
Plastic extrusion for efficient, scalable manufacturing solutions
Blog Article
Secret Advantages and Factors To Consider of Carrying Out Plastic Extrusion in Your Jobs
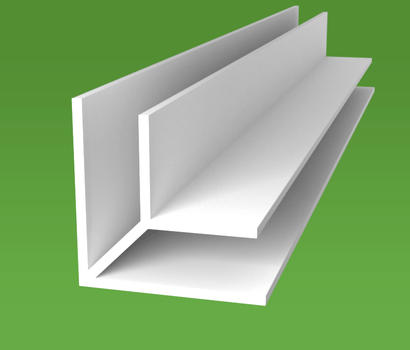
Understanding the Fundamentals of Plastic Extrusion
Plastic extrusion, a staple in the production market, is a process that involves melting raw plastic product and reshaping it right into a constant profile. This account, once cooled, can be reduced into wanted lengths or curled for later use. The elegance of plastic extrusion depends on its adaptability. A large range of products, from piping to home window frames, can be generated. The procedure calls for an extruder, a detailed maker with a warmed barrel, a turning screw, and a die at the end. The plastic material, in the form of pellets, is fed into the extruder, where it's melted and required via the die, taking its shape. The selection of plastic and the layout of the die establish the product's features.

The Economic Benefit of Plastic Extrusion
The economic benefit of plastic extrusion lies primarily in two locations: cost-effective material manufacturing and valuable production rates. With plastic extrusion, services can create high quantities of material at a lower cost contrasted to other approaches. The process flaunts a remarkable production speed, significantly reducing time and additional improving its financial stability.
Economical Product Production
A considerable advantage of plastic extrusion is its exceptional cost-effectiveness. This manufacturing process allows for constant, high-volume production with minimal waste, which translates into reduced costs. The raw products used, usually plastic pellets, are relatively inexpensive contrasted to various other substances (plastic extrusion). The procedure itself calls for much less energy than several other manufacturing methods, better reducing prices. Additionally, the extrusion process permits a high level of accuracy in forming the plastic, decreasing the demand for expensive post-production changes or corrections. Additionally, the durability and longevity of extruded plastic products typically mean less require for replacements, adding to long-term financial savings. All these variables make plastic extrusion a highly cost-effective selection for several tasks, supplying an eye-catching equilibrium in between cost and performance.
Beneficial Manufacturing Speeds
While maintaining the cost-effectiveness of the products, one more notable advantage of plastic extrusion exists in its rapid manufacturing speeds. This effectiveness in the manufacturing procedure is connected to the continual nature of the extrusion procedure, permitting high-volume production in a reasonably brief time period. The rate of manufacturing straight correlates to a decrease in labor prices and an increase in result, therefore improving the overall economic practicality of the procedure. The hectic manufacturing does not compromise the high quality of the last item, ensuring constant and trusted outcomes. This mix of cost-effectiveness, high quality, and speed underscores the considerable financial benefit of applying plastic extrusion in numerous projects.
Flexibility and Personalization: The Toughness of Plastic Extrusion
One click for more info of the famous toughness of plastic extrusion hinges on its convenience and personalization capacity. These top qualities unlock to endless design possibilities, offering manufacturers the capacity to customize items to details needs. This increased level of customization not only enhances product capability yet likewise substantially enhances item individuality.
Unlimited Style Possibilities
Plastic extrusion radiates in its capability to use practically infinite design possibilities. Plastic hop over to here extrusion can handle a variety of plastic kinds, expanding its application scope. With plastic extrusion, the design possibilities are practically countless.
Increasing Product Uniqueness
The adaptability of plastic extrusion can considerably enhance product uniqueness. This process allows developers to try out different shapes, sizes, and colors, providing the freedom to create unique products that stand out on the market. It is this personalization that provides an unique identity to each item, identifying it from its rivals.
Along with its visual advantages, the customizability of plastic extrusion also uses sensible benefits. Designers can change the homes of the plastic according to the specific demands of the application, boosting the product's functionality. They can make the plastic extra versatile, a lot more long lasting, or much more immune to warm, depending on what the product calls for. Hence, plastic extrusion not just increases item uniqueness but additionally its utility and marketability.
Style Limitations in Plastic Extrusion: What You Need to Know
Exactly how can make restrictions possibly affect the procedure of plastic extrusion? While plastic extrusion is flexible, design restrictions can curtail its advantages. Specific complex styles try this might not be possible as a result of the constraints of the extrusion process, possibly restricting the development of intricate accounts. The process is less ideal for hollow or multi-chambered frameworks. In addition, the extrusion procedure might not always give the wanted surface coating, specifically for those calling for high gloss or optical clearness. Product selection can also posture obstacles, as not all polymers are suitable for extrusion. High-temperature resistant plastics, for circumstances, might offer troubles. Understanding these restrictions is crucial for effective application of plastic extrusion in your projects. plastic extrusion.
Evaluating the Ecological Effect of Plastic Extrusion
While recognizing style restrictions is a substantial aspect of plastic extrusion, it is equally essential to consider its environmental implications. The process of plastic extrusion includes melting plastic materials, potentially releasing hazardous gases into the setting. Further, the resulting products are often non-biodegradable, adding to land fill waste. Nonetheless, developments in modern technology have actually permitted more environmentally-friendly techniques. For example, utilizing recycled plastic materials in the extrusion procedure can minimize environmental impact. In addition, establishing naturally degradable plastic choices can aid reduce waste issues. Reviewing these environmental elements is important when executing plastic extrusion tasks, making sure a balance in between efficiency, cost-effectiveness, and ecological obligation.
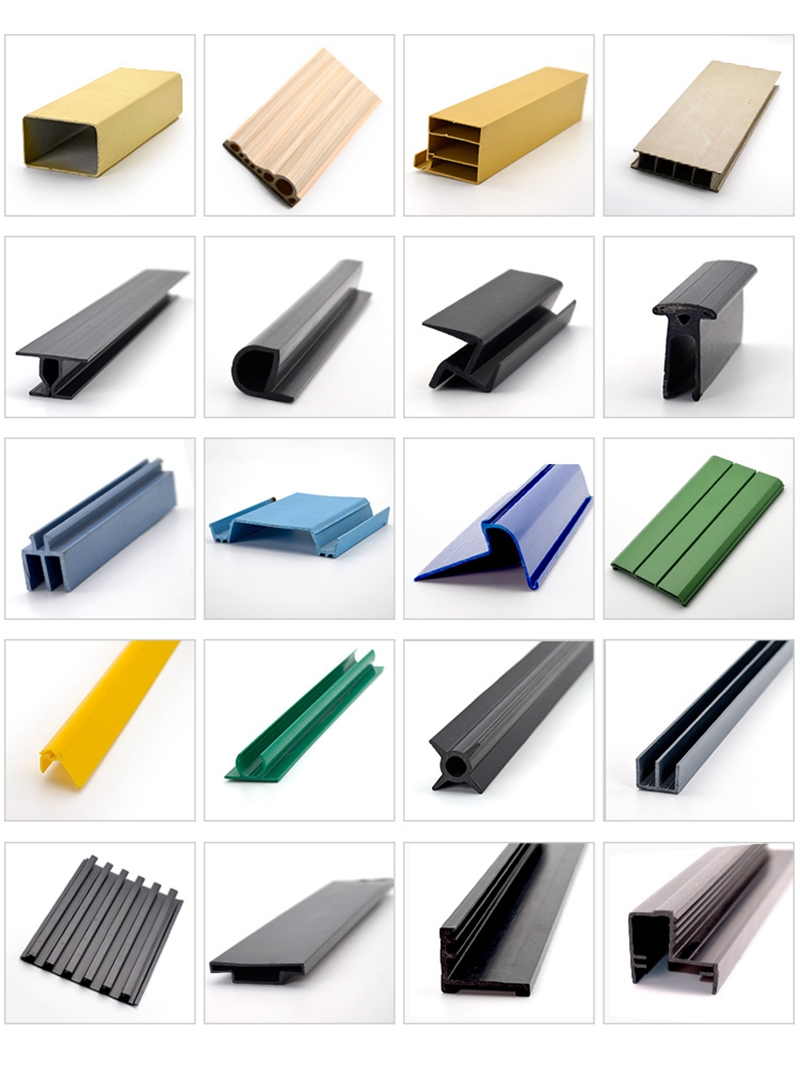
Study: Effective Projects Using Plastic Extrusion
Success tales in the field of plastic extrusion abound, demonstrating both the flexibility and effectiveness of this manufacturing process. plastic extrusion. One more successful instance is the manufacturing of plastic movie for product packaging and farming. These circumstances illustrate plastic extrusion's essential role in different industries, testifying to its versatility, cost-effectiveness, and reputable result.
Conclusion
In final thought, plastic extrusion uses a effective and cost-effective method for producing complicated shapes with marginal waste. While it offers many advantages such as cost-effectiveness and flexibility, it's important to take into consideration possible design limitations and ecological results. Executing biodegradable or recycled products can reduce these issues, enhancing sustainability. Including plastic extrusion into jobs can cause successful outcomes, as shown by countless instance researches.
Plastic extrusion, a staple in the production sector, is a procedure that involves melting raw plastic product and improving it right into a continuous account. Plastic extrusion can handle a range of plastic kinds, increasing its application range.How can make limitations potentially influence the procedure of plastic extrusion? The process of plastic extrusion involves melting plastic products, possibly releasing damaging gases into the setting. Using recycled plastic materials in the extrusion process can minimize environmental impact.
Report this page